Installation Process
a. | Clean area from Dust and Stickings as best as possible by high pressure air. The affected areas were cleaned well with compressed air. All loose adhesions and dust deposits were also removed as much as possible by this process. The repair areas prepared in this way are usually divided into installation fields. |
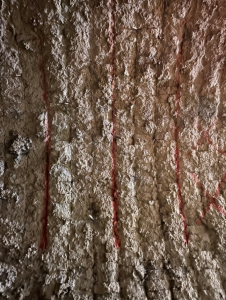
b. | REFKO RECOVERY Anchor for thickness >40-50mm. Depending on the desired layer thickness, the use of anchors can also be considered. This must be decided individually ‘on site’. REFKO does not recommend gun layers below 5 cm thickness. |
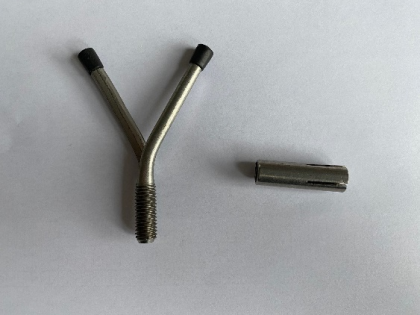
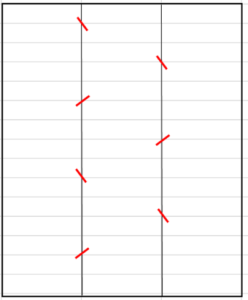
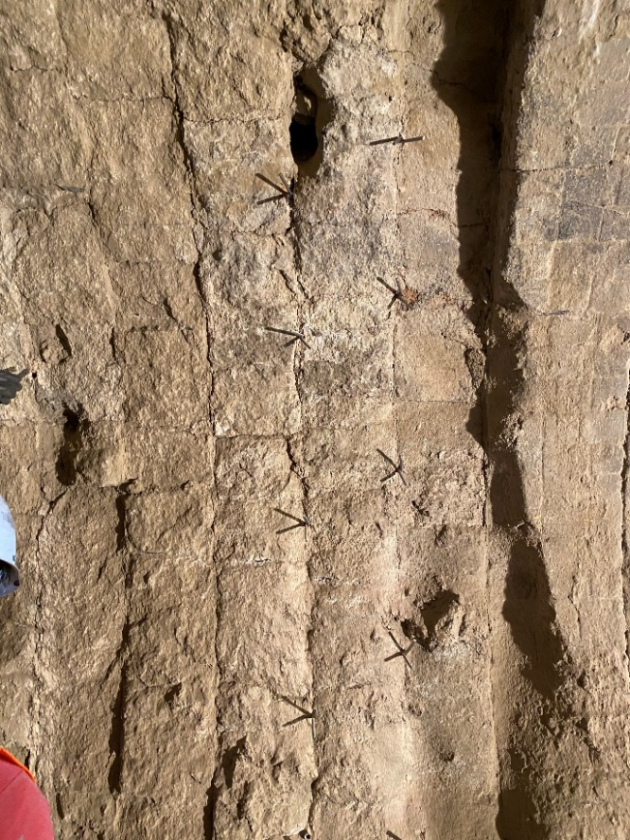
Media1 - Page 3 2 20 3 Monolithic Refractories -Cement Industries
(Refko Veneering Installation)
c. | Formwork & separation in fields (like recommended for all monolithic installations). The installation fields are separated from each other by working joints and the joints should follow the stone joints. This is necessary to give flexibility to the mechanical loads in the heating up and operational phase, as well as the thermal expansion of the monolithic layer. To achieve optimal mechanical stability, complete rings should always be gunned. The selective repair of damaged areas is not advisable.
|
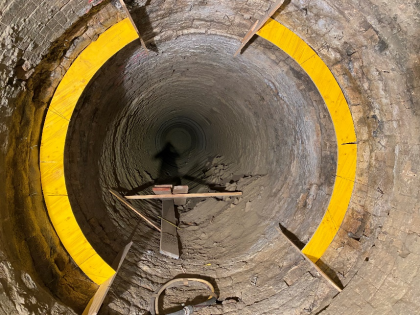
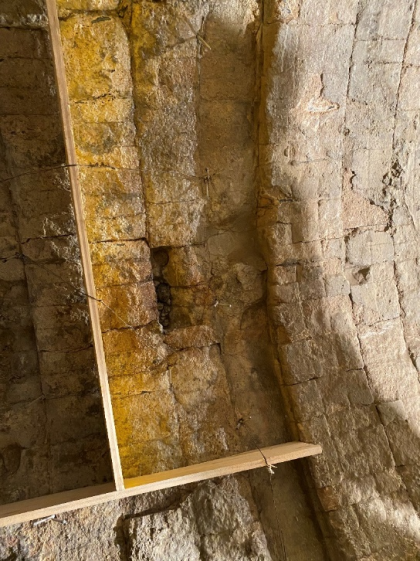
d. | Gunning Process.
The gunning of the REFKO Recovery MG concrete was carried out in this case with a commercially available dry- or respectively rotor-gunning machine. These machines are in use worldwide and can be easily organized for emergency repair work. The REFKO Recovery products do not require any special machines that can only be operated by specialists. The only special feature is the use of a high-pressure membrane spray nozzle, or the ‘REFKO nozzle.’ In combination with a high-pressure water pump, a practically dust-free gunning installation can be achieved and this special refractory concrete can be gunned with good results. The REFKO nozzle and high-pressure water pump are now standard in many cement plants and installation companies. If, however, no REFKO nozzle and/or high-pressure pump are available, equipment will be provided by REFKO. |
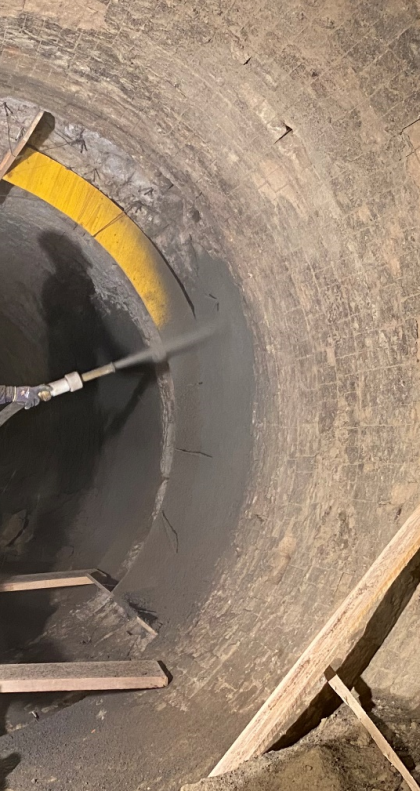
Media2 - Page 3 2 20 3 Monolithic Refractories -Cement Industries
(Refko Veneering Installation)
After installation
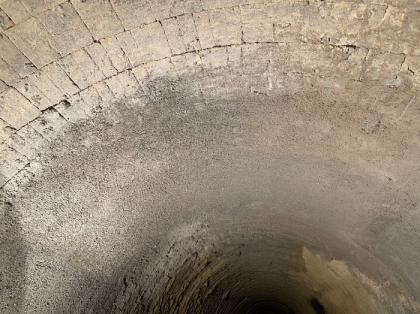
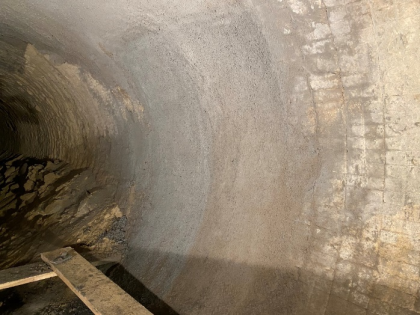
After setting, the concrete developed a stable connection with the subsoil, so that the furnace could be turned to the next mounting position without any problem. REFKO had to deal with very low outside temperatures, but even under these conditions, the concrete could be safely installed.
24 hours after completing the gunning, the kiln was ignited again. The binding system of the REFKO Recovery MG System also allows for a quick restart of the furnaces. Furnaces can be heated according to the respective plant-specific specifications for re-starting.
The heat-up to operating temperature and the first material feed in the repaired area went ahead without any problem. No material spalling was detected in the kiln during the start phase.
After reaching the operating temperature, the repaired zone was monitored with thermal cameras throughout the whole Cleaned surface and marking of the installation fields.
News & Publication by Refko Feurfest Germany
- Saving Time and Money by Herbert Hönl, Refko Feuerfest GmbH, Germany on World Cement 2015
- Relieving Mechanical & Chemical Stress by Herbert Hönl, Refko Feuerfest GmbH, Germany on World Cement 2014
- In the Line of Fire by Herbert Hönl, Refko Feuerfest GmbH, Germany on World Cement 2011
- Ready for Rapid Recovery & Repair by Herbert Hönl, Refko Feuerfest GmbH, Germany on World Cement September 2021
Please visit website www.refko.de
Monocrystal (Single) Fused Alumina Product
Monocrystal (Single) Fused Alumina Product is produced from high purity Bayer Alumina.